Oil Filter
Magnet
"Consumer Kit" #80-1144-C10
Magnets are available
for consumers that do their own oil changes or want to take them
personally to a technician for installation.
Custom packaged 10 Oil Filter Magnets and simple instructions
Order part number... #80-1144-C10
Cost is just $19.95
(Plus a small shipping
charge)
Call GWR at 1(800) 266-4497
(Order Desk is open
from 2pm to 8pm EST)
Wait,
isn't it better to put a big wrap around magnet on
my oil filter ???
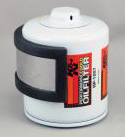
Well if
you're comparing an expensive wrap around oil filter
magnet to our patented internal magnets, please
consider this. |
|
FACT: If
you wrap their bulky, heavy Filter Magnet around
your cartridge,
you will pull tons of metal out of your oil. |
|
SPOILER ALERT... |
The media
paper in your oil filter could have done the same
job for free!
|
Yikes!
You just spent $50 on their fancy looking magnet for
nothing.
|
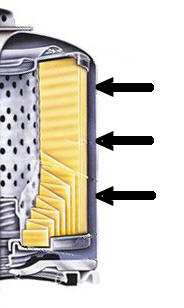

|
Let's
take a look at the center picture, a cut open oil
filter
wrapped in an external Filter Magnet type product.
Where is all the
metal deposited?
|
You are
being tricked by these types of photos because they
show the larger metal particles that have not
reached the oil filter element yet. Remember that if
you can see metal it is larger than 50 microns, so
all of these loose chips of metal would have been
caught by the paper media.
|
Truth is
you should never collect metal before it passes into
and through the media. What you want to collect with
a magnet is any particles that are so small, they go
through the media. The ones that are 5, 10 or 15
microns, the ones the SAE documents below say are
responsible for 80% of your engines wear.
|
A more
important issue is engineering! These products are
in direct conflict with the design an OE Filter
company builds into their products.
|
Note
above that oil flows from the outside to the inside
of filter but also note the space between walls and
media paper, it is extremely tight and narrow.
|
Now note
where the ragged, rough large metal particles are
deposited. They all end up in nice little rows along
the inner wall of the filter's metal shell. Well
those walls are factory finished with high tech
paint like coatings that seal and smooth the raw
steel so it is virtually a zero friction component.
FACT: The faster and easier the oil flows up
the side wall and then into the paper media, the
less Horse Power (ie Gasoline) it takes to pump the
oil.
|
The last
thing you or the filter manufacturer wants is a
rough surface on the inside of that can, it just
does not make good sense on any level. Let the
filter do it job of removing larger particles and
then let our Ceramic Oil Filter Magnets clean up
what the spin-on unit misses... it's a winning
combo! |
Call GWR
at 1(800) 266-4497
(Order Desk is open
from 2pm to 8pm EST)
For
the techies in the group... here is what you are looking for!
SOME
IMPORTANT TEST RESULTS
* SAE Technical Papers:
881827, 881825, 952555 & Additional Scientific Studies
Lube oil contamination accounts for seventy to eighty percent
of all failures and wear problems. The wear process promoted by
oil contamination leads to diminished fuel efficiency,
shorter useful oil service life, increased engine down
time, reduced component life, loss of engine
performance, and an overall increase in operating costs.
Contaminant particles responsible for this damage are in
the size range of the dynamic lubricant films separating moving
engine component surfaces... 10 microns and smaller.
Typically these particles pass through the oil filter and
continue to build up in the oil system. By making simultaneous
contact with opposing surfaces these harmful particles focus the
load onto a small area, degrading the surface and perpetuating a
chain-reaction-of-wear.
There are three categories of oil contaminates active in the
engine wear process:
1. Solid particles, including wear debris and soot, which
damage mechanical components and catalyze lubricant breakdown;
2. Liquid contaminates, including fuel and water, which corrode
metals and hinder the functioning of lubricants; and
3. Gaseous contaminants, including acidic combustion products,
which corrode component surfaces and degrade the oil.
The predominant harmful impurities in engine oil are
metallic particles and metal oxides. Typically there are
well over 10,000 contaminant particles per milliliter of lube
oil. Furthermore, approximately 90% of these particles are
less than 10-microns in size. It's important to note that
these particles generate about 3.5-times more wear than
particles greater than 10-microns in size. This wear occurs
because these particles are the size of, or slightly larger than
the dynamic oil films separating opposing surfaces.
Numerous studies have established a number of important
points regarding the relationship between lube oil contamination
and engine wear.
In the following SAE Paper 881827 substituting a standard 20-30
micron filter with a 10-micron filter resulted in:
1. A reduced concentration of contaminant particles by a
factor of 10-15 times;
2. A reduction in the four major wear metals monitored;
3. The filter was capable of operating more than twice the
recommended service life; and
4. The lube oil service life to be more than doubled without
adverse engine wear or lubricant degradation.
In summary, controlling particle contamination in the 1-10
micron size range retards the chain-reaction-of-wear, resulting
in significant reductions in component wear and lubricant
breakdown. The beneficial consequences include greater component
life and reliability, increased oil change intervals, increased
fuel efficiency, and a reduction in overall maintenance costs.
Diesel Component Wear Test
on DDA 6V-53T Engine
(Performed by AC Delco Division of General Motors / GM)
Five critical component areas were tested:
1. Upper & Lower rod bearings.
2. Slipper bushings.
3. Compression & oil piston rings.
4. Piston rings.
5. The main bearings.
A. Diesel Engine Wear and Fuel Economy:
A study of twenty-two 6-cylindar diesel engines performed by
Fodor & Ling
(affiliated with the Research Institute of Automotive
Industry-Budapest and the Rensselaer
Polytechnic Institute)
Conclusion: Control of particles in the 3-10 micron range
had the greatest affect in reducing engine wear.
It was found reducing contamination from 0.016% by weight
(standard oil filter) to 0.0025% by weight (extended filter / 10
micron control), reduced engine wear by a factor of 14. Most
significantly, oil friction was reduced by 2.9% compared to
operating with clean oil. This reduction was equated to an
increase in fuel economy of about 4%. As a comparison, this
significantly exceeds the 0.6 - 0.9% fuel economy gain
experienced when converting from SAE 40 to multi grade lube oil.
B. Survey of Diesel Engine Oil Contamination Levels
Samples of 138 engines operating with standard paper filter
were compared to 117 engines operating with upgraded 10-micron
filters.
Conclusions:
Based on the relationship difference between dynamic oil
film and size of wear generating particles, the most important
particle size range is 0-10 microns.
1. Diesel engine lube oil contamination causes wear of engine
components. Wear of these components leads to loss of
performance, increased maintenance and overhaul cost, lower fuel
efficiency, and shorter lube oil service life.
2. There is a fundamental relationship between the size of
contaminate particles and the thickness of the dynamic oil films
developed between moving surfaces of active components.
Particles the size of, or smaller than, the oil film thickness
cause wear of components. By making simultaneous contact with
both surfaces, these particles focus the load onto a small
region of the surface, resulting in surface pitting, plowing,
and cutting.
3. The average oil film thickness associated with the majority
of diesel engine components is in the 7 to 10 micron size
domain. This is the size range of the most damaging contaminant
particles. In addition, mechanical stress is accentuated during
the high-load/thinner oil film phase of the engine cycle. In
order to minimize engine wear, emphasis must, therefore, be
placed on controlling particles in the 10-micron size domain and
smaller.
4. Oil contamination causes component wear and in return,
generates more contamination. This is the
chain-reaction-of-wear. If uncontrolled, this process results in
an enormous number of oil suspended particles. The consequences
of uncontrolled chain-reaction-of-wear are:
a) Higher friction, leading to high fuel consumption.
b) Loss of material from sliding and rolling contacts, resulting
in misalignment, vibration, and component replacement.
c) Opening of piston dynamic sealing surfaces, leading to loss
of compression, further fuel consumption, and contaminant
ingestion from the environment.
d) The accumulation of soot and combustion products in the lube
oil and the formation of lubricant breakdown varnishes and
sludge leading to reduced oil service life.
5. The significance of proliferating particles in the
10-micron range domain is phenomenal. Each grain of
contaminant (wear debris, mineral grain, metallic oxide)
produces a small but finite amount of friction, abrasive wear,
and catalytic oil breakdown. Because of the vast number of
harmful particles, the total effect of this multitude is
abbreviated oil life, substantially higher engine friction, and
propagation of engine wear
6. The benefits of controlling oil cleanliness levels to the
order of 100-1000 particles /ml (10 times reduction) are:
a) An 8 to 14 times reduction in engine wear.
b) Up to 2 times increase in oil service life.
c) Up to 2 times increase in filter service life.
d) Up to 5% improvement in fuel economy.
The ultimate benefits are greater diesel engine
performance over extended life with lower operating cost.
Independent Laboratory Test
by Titan Labs
The subject was a Peterbuilt engine (CAT C12) using a Premo
LT-30P oil filter system equipped with a 1.2 micron filter. A
baseline test was performed at an interval of 15,000 miles as
indicated on the Analysis Report dated 4/11/01. Ceramic Oil
Filter Magnets were then inserted into the oil filter. After
15,000 miles, the second test was performed on 4/30/01.
Please note the dynamic improvement in ferrous particle
reduction (in PPM), but also non-ferrous materials/contaminants
by the process of heterocoagulation. Final column is percent
of change from 1.2 Micron super filter system that costs over
$250 and is 25 times better than any standard street vehicle
filter.
Tests conducted by:
Titan Laboratories, Denver, CO
Oil analysis report measuring parts per million (PPM), particle
size 0.5 microns.
Elements
Tested
|
Ferrous* |
PPM "Before"
Oil Filter Magnet
|
PPM "After"
Oil Filter Magnet
|
Percentage
Reduction
|
Boron |
Non |
3
|
2
|
33%
|
Calcium |
Non |
2,929
|
2,870
|
2%
|
Copper |
Non |
345
|
255
|
26%
|
Iron |
|
57
|
13
|
77%
|
Lead |
Non |
5
|
1
|
80%
|
Magnesium |
Non |
14
|
2
|
86%
|
Phosphorus |
Non |
1,533
|
1,104
|
28%
|
Silicon/Silica |
Non |
40
|
8
|
80%
|
Sodium |
Non |
264
|
37
|
86%
|
* IMPORTANT FACT
Even Non Ferrous (Non Magnetic) particulate are pulled in by
our Oil Filter Magnets!
The friction reduction improvement caused by removal of
Ferrous plus Non Ferrous (the total particulate count)
is why you can improve fuel economy if you include an Oil
Filter Magnet in every oil change.
As demonstrated by SAE Technical Papers (listed above), the
benefits of oil particle reduction in the 10 micron range are:
An 8 to 14 times reduction in engine wear.
Up to 2 times increase in oil service life.
Up to 2 times increase in filter service life.
Up to 5% improvement in fuel economy.
The ultimate benefits are greater engine performance over
extended life with lower operating costs and higher resale
value.
GWR Oil Filter Magnets can be added to virtually any oil
filter and control particle contamination down to 0.5-microns.
This is a 20-times improvement in particle control as compared
to the SAE Technical Papers that indicate substantial wear
reduction and fuel improvement by control down to only 10
microns.
Companion product you will want to see....
Automotive Link
to Fluid Analysis Systems
Another tip to save
gasoline and tire wear, be sure to put...
Nitrogen in tires
|